JHIMS·460 | PCB SPI Solder Paste Inspection Machine
Ⅰ、Introduction:
The programmable structured grating technology (PSLM PMP) uses PSLM components with cutting-edge German technology. [Ten-year free warranty]
1. The grating period is modulated by software. Different structured grating periods can be provided.
2. The phase change of the structured grating is controlled by software, without any mechanical transmission parts. No loss.
3. The effective detection height can be adjusted without adding any parts. (400um to 1200um software adjustable)
4. Because the sinusoidal grating of the programmable structured grating is realized by software programming, its phase shift is also realized by software. Through this technology, the phase shift error can be tended to "0", which improves the
Ⅱ、Product Features:
1、The use of PSLM combined with the PMP to achieve 100% high- precision solder paste 3D measurement in SMT production line. Using PSLM technology, changed the traditional way of generating 3D Struct Light, the traditional glass grating moire (Moiré) required mechanically driven by a piezoelectric motor (PZT). By using PSLM, no need glass grating and mechanical parts any more. The elimination of the mechanical drive and moving parts, greatly improving the ease of use and avoid mechanical wear and reduce maintenance costs.
2、By using the Stop & Catch methods combined with multiple image acquisition, realize highly repeatable 3D results on the solder paste measurement. Compared to conventional scanning just take one pictures only on the solder paste a scan sampling, multiple image acquisition greatly enhancing the accuracy and reliable test results.
3、Patented D-Lighting technology achieves full light spectrum detect ability. It is perfect solution to solve the shadow effect and reduce noise interference during 3D measurement.
4、Gerber data conversion and import, achieve automatic detection of the entire board. Manual "Teach" function realize user-friendly programming and test job generation in case of no Gerber data situation.
5、The maximum detectable height increased from the traditional ± 350um to ± 1200um, not only can detect solder paste, also applies to the detection of opaque objects such as red glue and black epoxy and other none transparent object.
6、Friendly and simple user interface, five minutes of programming and one key operation.
7、Powerful "Statistical Process Control (SPC), provide a plenty of tools, user-friendly real-time monitoring, reduce defects caused by poor solder paste printing and improve final product quality.
Ⅲ、S460 Solder Paste Inspection Machine Parameters
Parameters |
Product Describtion |
Cost-Effective Model |
Series |
S460 |
Measurement Principle |
3D white light PSLM PMP(Programmable Spatial Light Modulation,commonly known as moire fringe technology) |
Measurements |
volume,acreage,height,XYoffset,shape |
Detection of Non - Performing Types |
missing print,insufficient tin, excessive tin, bridging, offset, mal-shapes, surface contamination |
Camcra Pixel |
5M |
Lens Types |
Telecentric lens + coaxial light |
Lens Resolution |
16um,13um |
Minimumelement |
British 0201 |
Accuracy |
XY(Resolution):1um;(Height):0.37um |
Repeatability |
height:<1um(3Sigma);volume/acreage:<1% (3Sigma) |
Gage R&R |
<10% |
FOV速度 FOV Speed |
0.45s/FOV |
Quantity of Inspection Head |
Single Head |
Red Green Blue/RGB Three Colas Option Light Source |
standard configuration |
Mark-point Detection Time |
0.5sec/piece |
Compensation Plate Bending of Real-time Lift in Z-axis |
standard configuration |
Maximun Meauring Height |
±550um(±1200um as option) |
Maximun Measuring Height of PCB Warp |
±5mm |
Minimum Pad Spacing |
150um |
Maximum Loading PCB Size |
L460xW460mm |
Thickness of the PCB |
0.4-7mm |
Height Limitations of the Parts |
up:30mm down:40mm |
Board Edge Distance |
3mm,multifunctional clip edge as option |
Flixble or Fixed Orbit Setting |
frontorbit(back orbit as option) |
PCB Transfer Direction |
left to rightor right to left |
Orbit Width Adjustment |
manual/automatic |
SPC Statistics |
Histogram: Xhar-R Chart; Xhar-S Chart; CP&CPK;%Gage Repartability Data;SPI Daily/Weekly/Monthly Reports |
Gerber & CAD Data Imput |
support Gerber format (274x, 274d) ,manual Teach model);
CAD X/Y,Part No.,Package Type imput) |
Industrial Personal
Computer
Configuration |
CPU |
Intel 17 |
RAM |
24G(32G as option) |
GPU |
2G diserete graphics(4G as option) |
Hard Disk |
IT |
Operating System |
Windows 7 Professional(64bit) |
Equipment Diemension and Weight |
1000x1150x1525mm,965KG |
Power Air Pressure |
220V、10A,4~6Bar |
Power(Start/nornmal) |
start: 2.5kw/normal operation : 2kw |
Loading Requirements of the Floor |
600kg/m2 |
Options |
multifunctional clip edge,1D/ 2D Barcode scanner, out//off-line programming software, UPS
continuous power supply、ultrasonic sensor |
Ⅳ、Z-axis profiling dynamic compensation
1. In actual applications, PCB boards will have more or less warp distortion (Warp Page).
2. Most SPIs are equipped with Z-axis automatic profiling function, which can detect the warping state of the PCB and automatically feedback to the servo mechanism according to the degree of warping to automatically adjust the height of the detection head to offset the warping distortion.
3.Flexible Printed Circuit Board (FPC), commonly known as FPC in the industry, is a printed circuit board made of flexible insulating substrate (mainly polyimide or polyester film). In the SMT process, it is generally fixed on the carrier with tape or frame for solder paste printing and patching.
4.Since SPI detection is based on each field of view window (FOV), each FOV may contain FPCs with different warpages, which makes the dynamic compensation based on the Z axis ineffective.
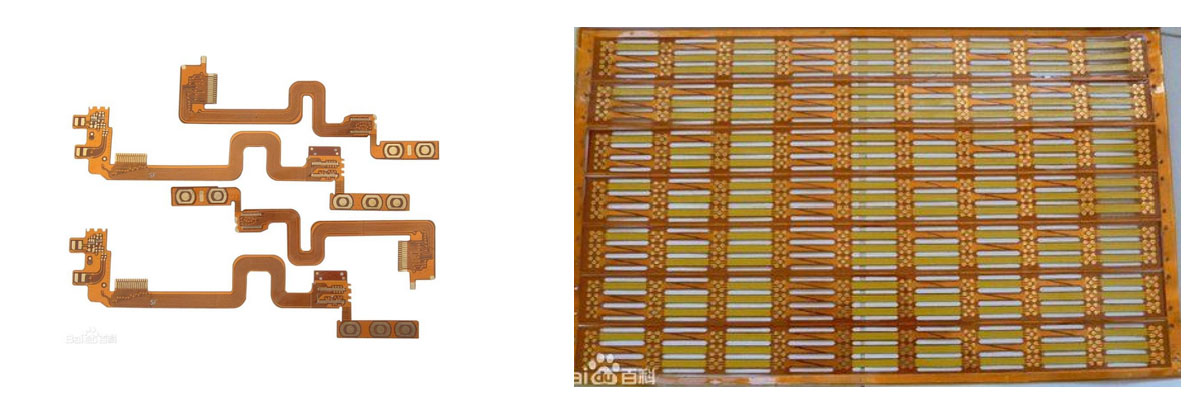
Ⅴ、SPI and printer closed-loop control function:
1. After SPI detects missing prints, it sends a command to the printer to clean the steel mesh; the printer automatically performs the steel mesh wiping and cleaning action;
2. SPI transmits the XY axis offset found in the test to the printer, and the printer determines whether correction is required after reading it (multiple pieces can be referenced and determined by the printer user); and executes the preset action to improve the printing quality.
3. Prerequisite: The printer needs to open the communication protocol to SPI, and the two parties have confirmed in advance that the data can communicate. At present, closed-loop control has been achieved with domestic printers such as GKG, Desen, and Right.
Ⅵ、Badmark information sharing between SPI and pick-and-place machine
1. SPI transmits the detected bad board information to the pick-and-place machine. After receiving the relevant information, the pick-and-place machine directly skips the bad board and picks and places it, saving the time for the pick-and-place machine to identify each sub-mark, greatly improving the mounting efficiency of multiple panels.
2. Implementation conditions: Since the information of each board needs to correspond one by one, a barcode must be mounted or printed on each PCB; SPI must be equipped with a barcode recognition module;
3. Prerequisites: The pick-and-place machine must open the communication protocol to SPI, and the pick-and-place machine must be equipped with the Badmark function that communicates with SPI; and the pick-and-place machine usually requires additional charges.